Production process
Production process in Aria Zob complex
The input of the product that is used as raw material in the Aria Zob complex is slabs and the output is hot sheets that are produced depending on the customer’s demand with different widths and thicknesses. In the following text, a part of the production process is described:
Slab cutting
: The input slabs are entered into the factory as raw material with dimensions of 1 to 2 meters in width and 6 to 12 meters in length and are cut by 8 CNC cutting tables to dimensions of 250-500 millimeters in width and 4, 6, 8 meters in length. Oxygen gas for air cutting is supplied by a 100 ton oxygen tank and LPG gas is supplied from a 6 ton LPG tank.
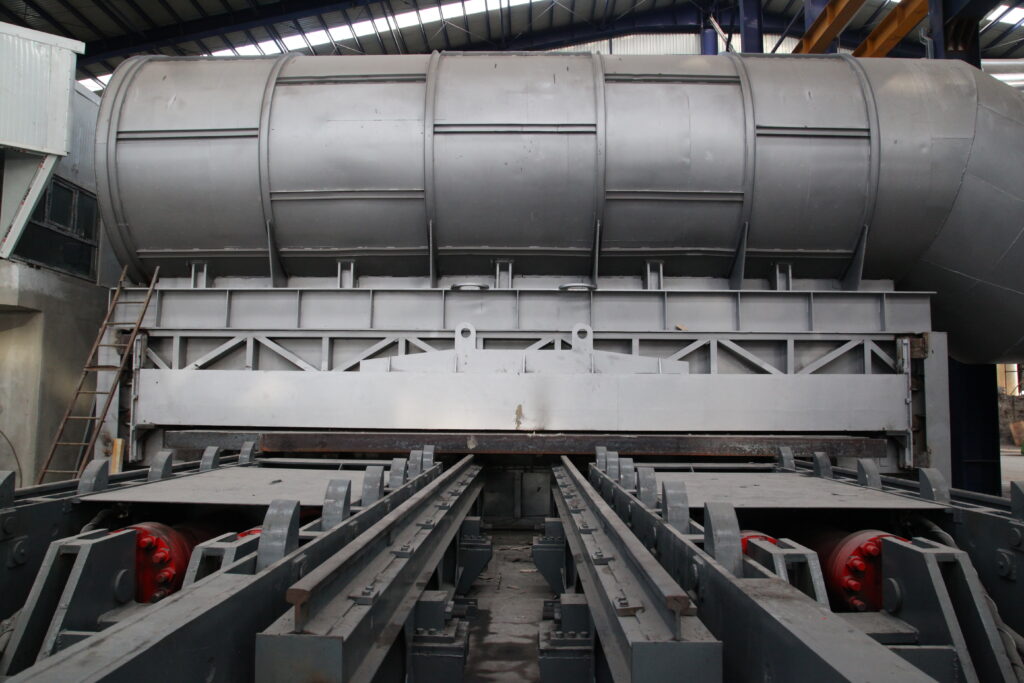
Pusher
Cut slabs are pushed into the furnace by nail pusher jacks.
Preheat oven
Preheated furnace with natural gas fuel with a capacity of 150 tons per hour, during a time of about 3 hours, the length of the furnace is 33 meters. The temperature of the ready slab and the temperature of the ready-rolled slab reaches about 1300 degrees Celsius.
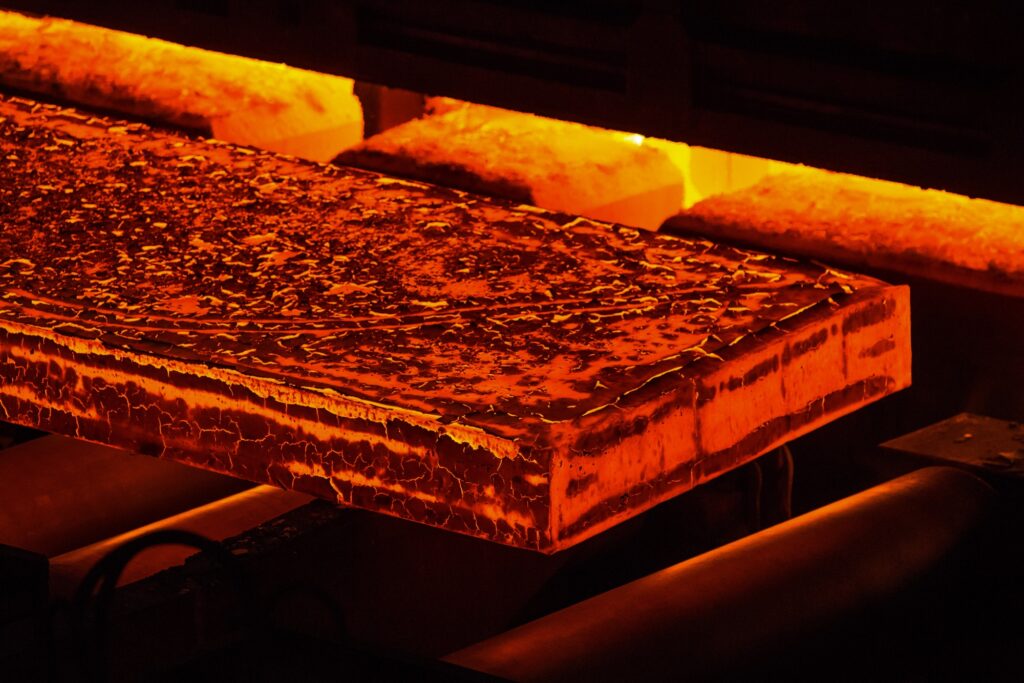
Unloader
By the hydraulic arms of 2 lift trucks, the ready-to-roll slabs are taken out of the furnace and placed on the rotating rolls.
Descaler or scaler
The rotating rolls take the slab into the descaler tunnel and with a working pressure of 250 bar, it destroys the oxide scales formed on the surface of the slab. The incoming water of the descaler is from the RO water purification system with a capacity of 300 cubic meters per day.
Ruffing
The slab is guided by the rotating rolls to the first rough rolling station (roughing) and during 5 round trips, the thickness of the slab has reached from 200 mm to about 30 mm, and the output of the roughing is guided to the next rolling stations by the rotating rolls.
Finishing rolling
The next steps of rolling by 12 vertical rolling stations (3 vertical and 9 horizontal) reach the product with thicknesses of 1.5 to 8 millimeters during the calculated reductions.
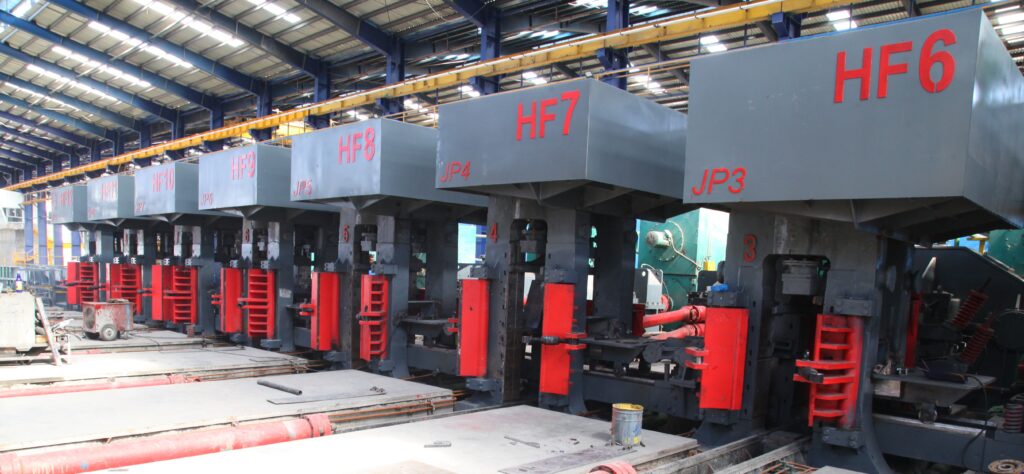
Termex
After leaving the last rolling station, the sheet enters the Thermox channel, where the surface of the sheet is oxidized and its temperature is reduced with high pressure water spray.
Cool bed
After thermoxing, the sheet is placed on the cooling bed in the form of a spiral by the Snaker machine, which includes two sets of separate chain wheel transmission, until the temperature of the sheet reaches about 500 degrees. Ken is 50 meters long.
Packaging
At the end of each cooling bed, the coiler (coiler) takes the sheet in the form of coils with a diameter of about 1500 mm with a tonnage of 2 to 6.5 tons, which is coiled by 40-meter long transfer rolls and belted by the machine. Automatic belt conveyor, a product warehouse is transferred.
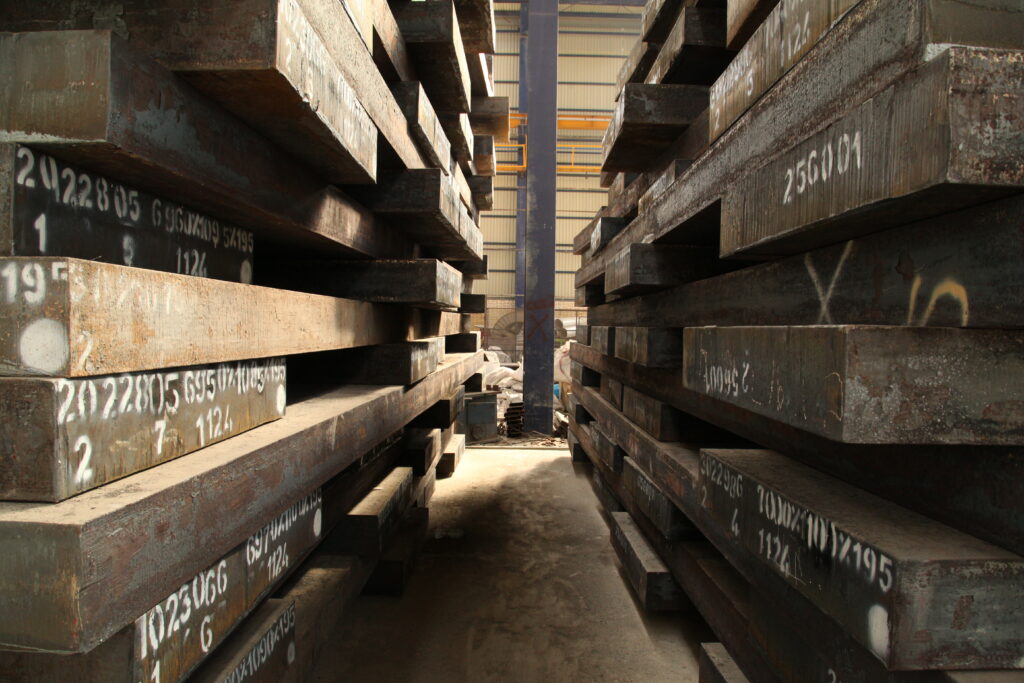
The water required for cooling the rolling machines is cooled by 7 cooling towers with a capacity of 500 tons per hour each.
The entire production process in the central operator is controlled by the full automation system and defects are monitored, recorded and recorded in order to prevent its repetition in the future and to ensure that the product is produced and transferred to the final warehouse.